What do commissioning jobs and projects in mechanical and plant engineering have in common? As a rule, these are complex processes that consist of several milestones and include numerous (sub) tasks. In addition, a large number of stakeholders is involved, working together across functions and sometimes even locations. It is precisely here that a clever and, above all, efficient coordination is more important than ever. Because nothing holds back progress more than...
- numerous meetings to discuss the current status
- delays due to lack of information or insufficient input from team members
- complex representation of tasks that are completed, upcoming or overdue
- no standardized and coordinated assignment of tasks
- missing documentation and verification
- responsibilities that are not clearly defined.
Service and project managers in the mechanical engineering sector will probably be familiar with challenges like this on a day-to-day business. As experienced commissioning engineer Jörg Stäudte from Meyer Burger reported: “The success of a commissioning job depends on preparation. If there were no surprises on site at the customer's plant, then that’s a clear indication that commissioning was a success.“ That’s because working together proactively is the key to successful projects and efficient processes.
To ensure this across the board and to support machine and plant manufacturers as well as their partners and customers, the Workflows module of EquipmentCloud® from Kontron AIS was developed based on Oracle Cloud Infrastructure (OCI) and the Oracle APEX Low-Code development platform.
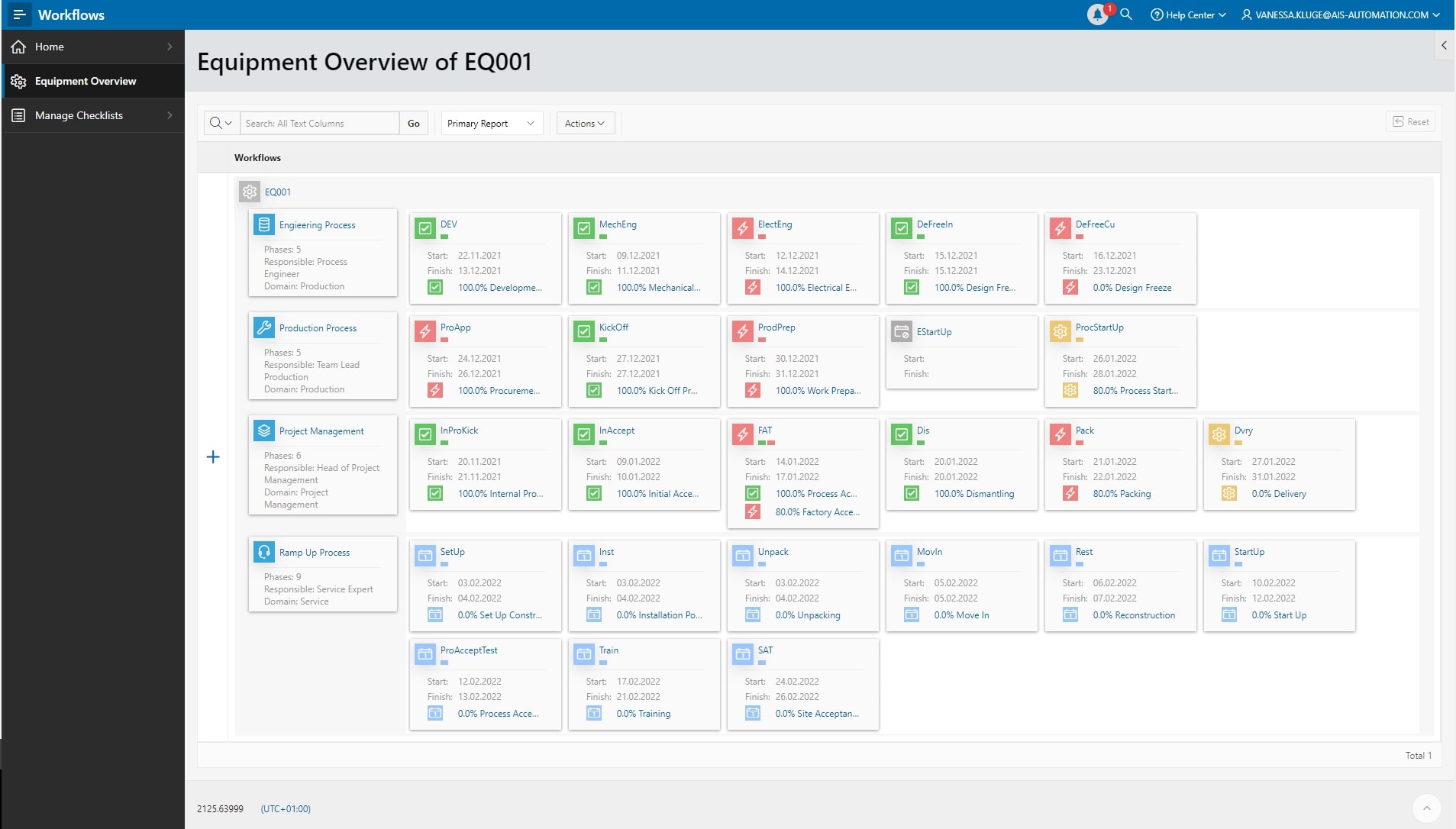
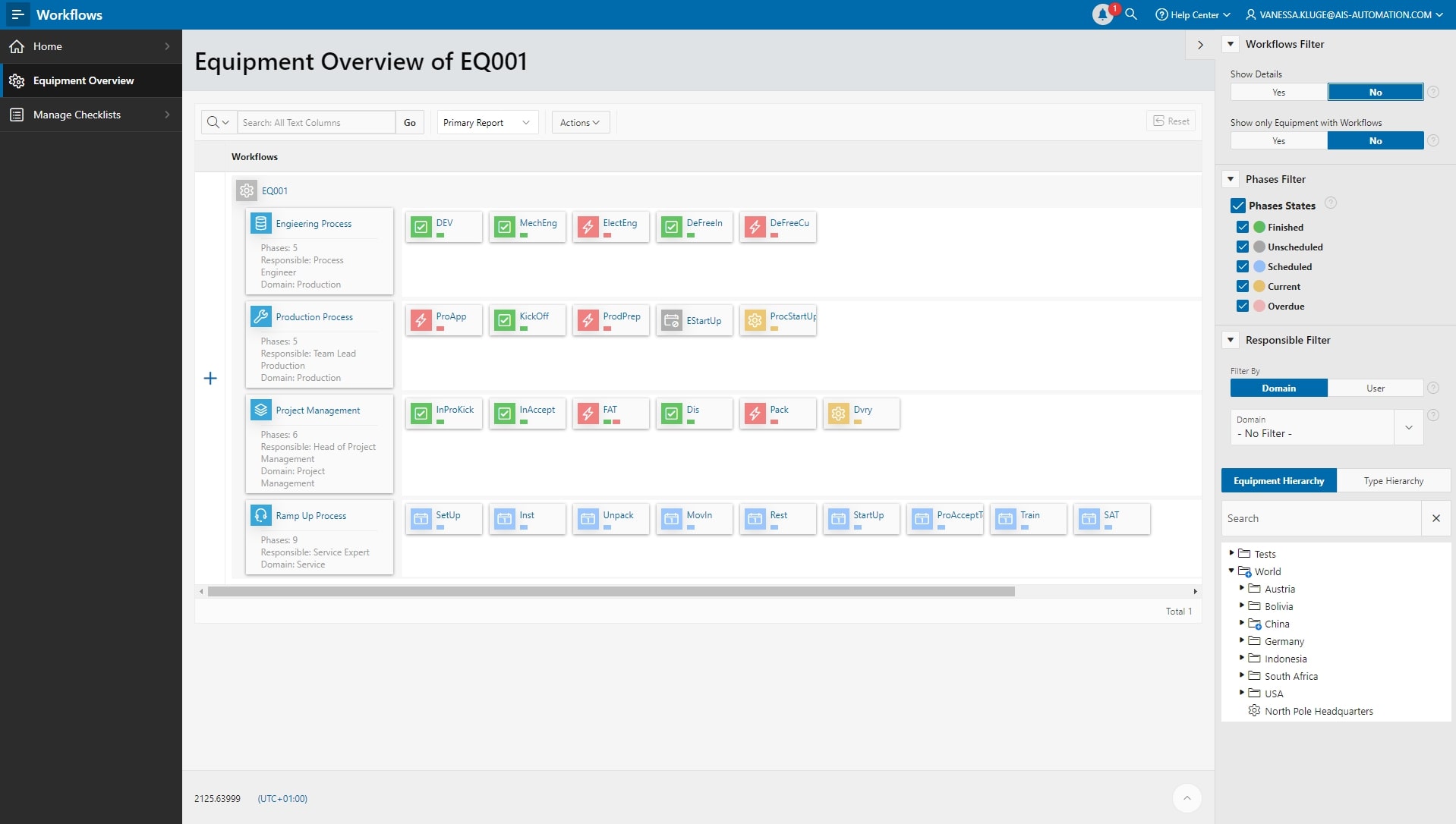
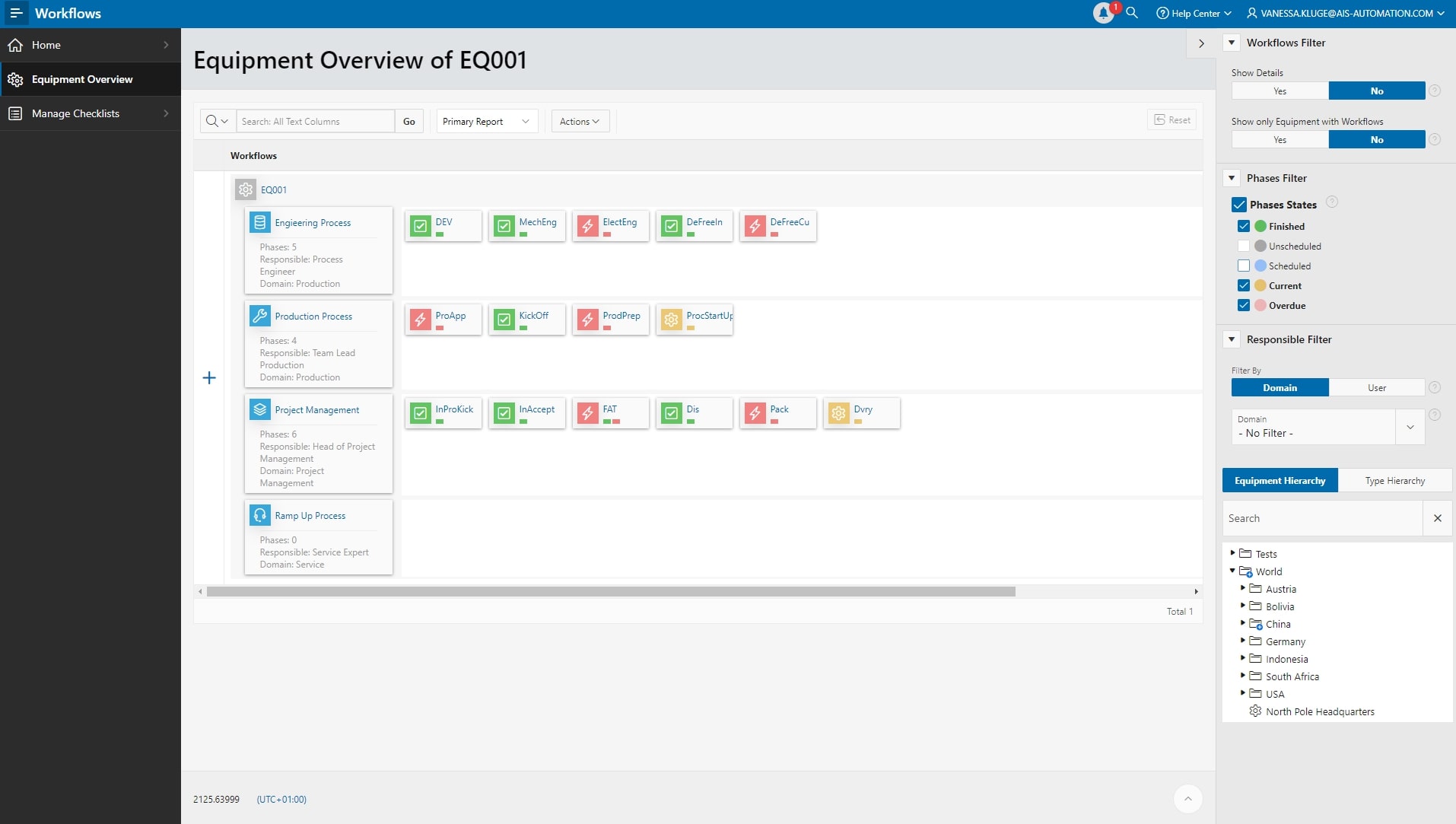
The new taskboard design makes the application especially dynamic. Each machine or project can be assigned multiple workflows, containing any of the milestones (phases) and/or associated checklists. In this way, processes running in parallel in different departments can be clearly separated from one another. At the same time, it is also possible to intelligently synergize processes that are actually separate using milestones and checklists.
A processing period including the due date can be set for each milestone. As the project progresses either through the completion of tasks or possible time delays, the current status of the respective checklist or milestone can be seen at a glance highlighted in color. Filtered views by level of detail and status provide a quick overview of the current process progress and upcoming tasks as well as possible delays.
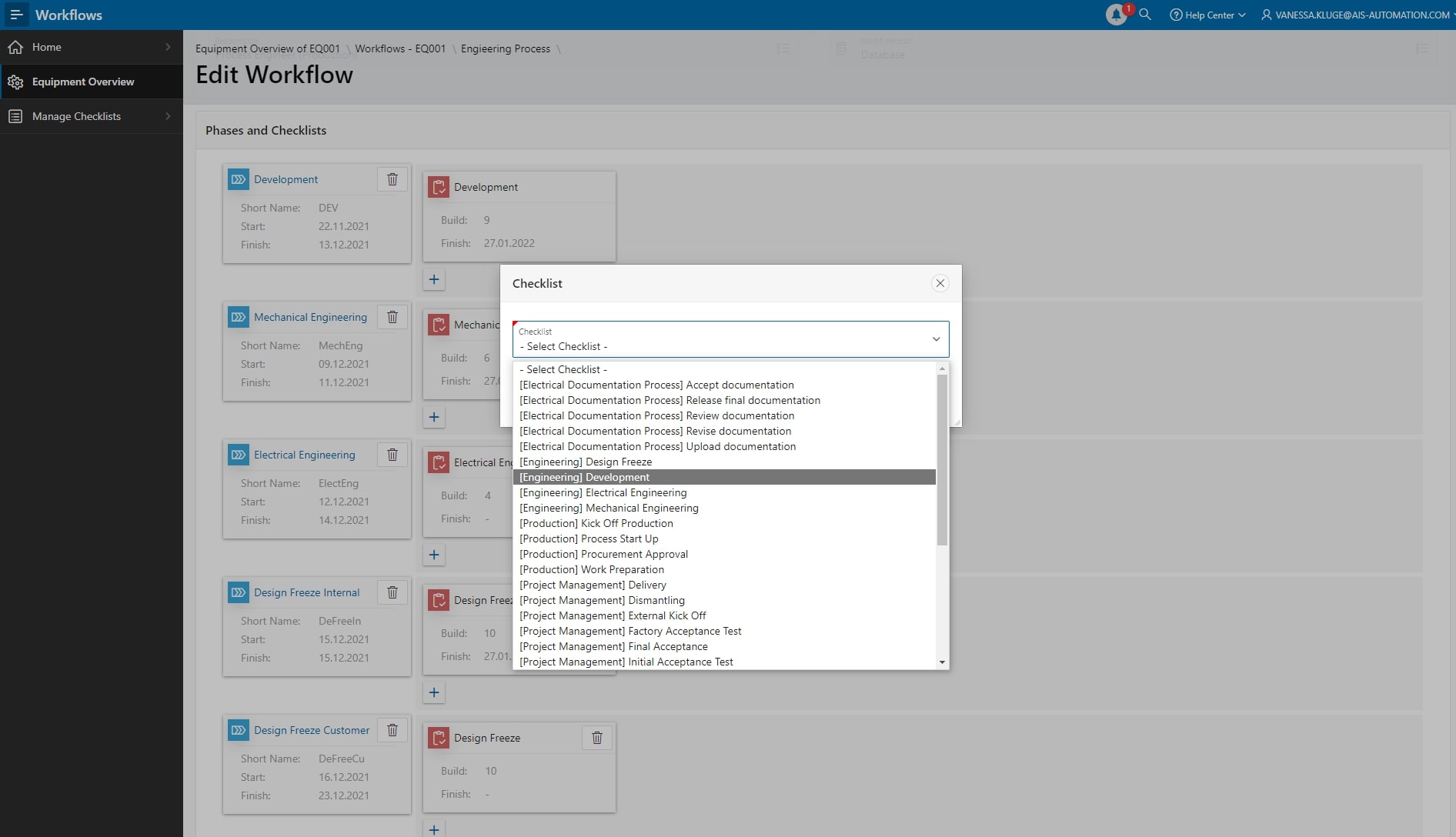
Repetitive processes are often composed of similar tasks or groups. They can be easily copied and flexibly combined in the designer, so that existing and proven workflows and checklists can be transferred to new machines of the same type or to sub modules of special machines without much effort.
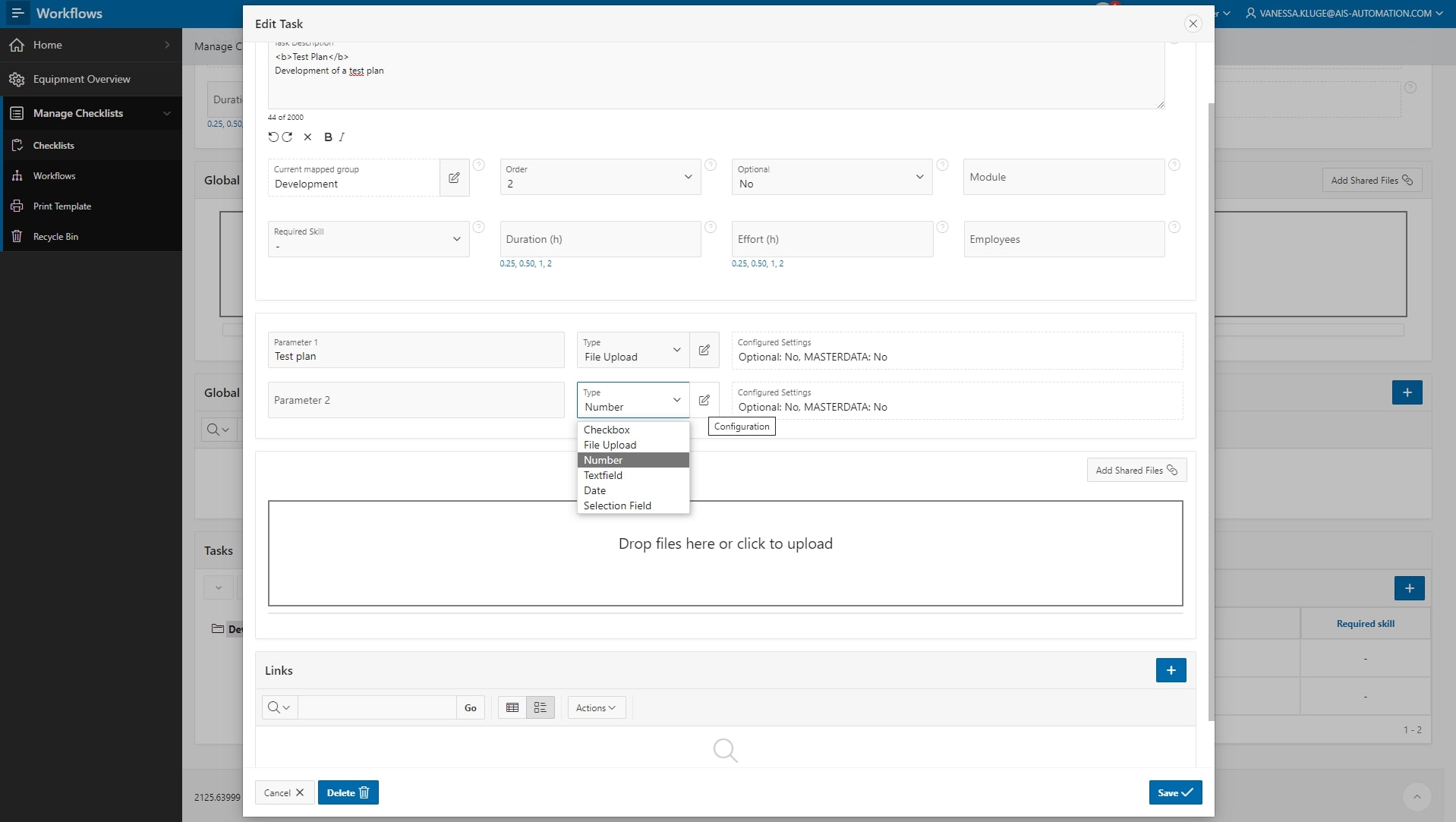
At the same time, digital checklists can be set up very specifically with different parameters (text field, checkbox, file upload, number field, selection field or date) for the individual tasks. They can also be reused over and over againrepeatedly times via so-called templates, not only in other workflows, but also in checklists of maintenance plans within the Maintenance module. During creation, it is already determined whether the checklists are available in both modules. The marking of optional tasks also allows specialist personnel to decide for themselves in each case whether the tasks are relevant. The assignment of modules to a task also makes it possible to display tasks only if this module is an actual part of the respective machine. Digital checklists can also be created very comprehensively this way, and then shortened to match the module during execution, which can significantly support the service employee.
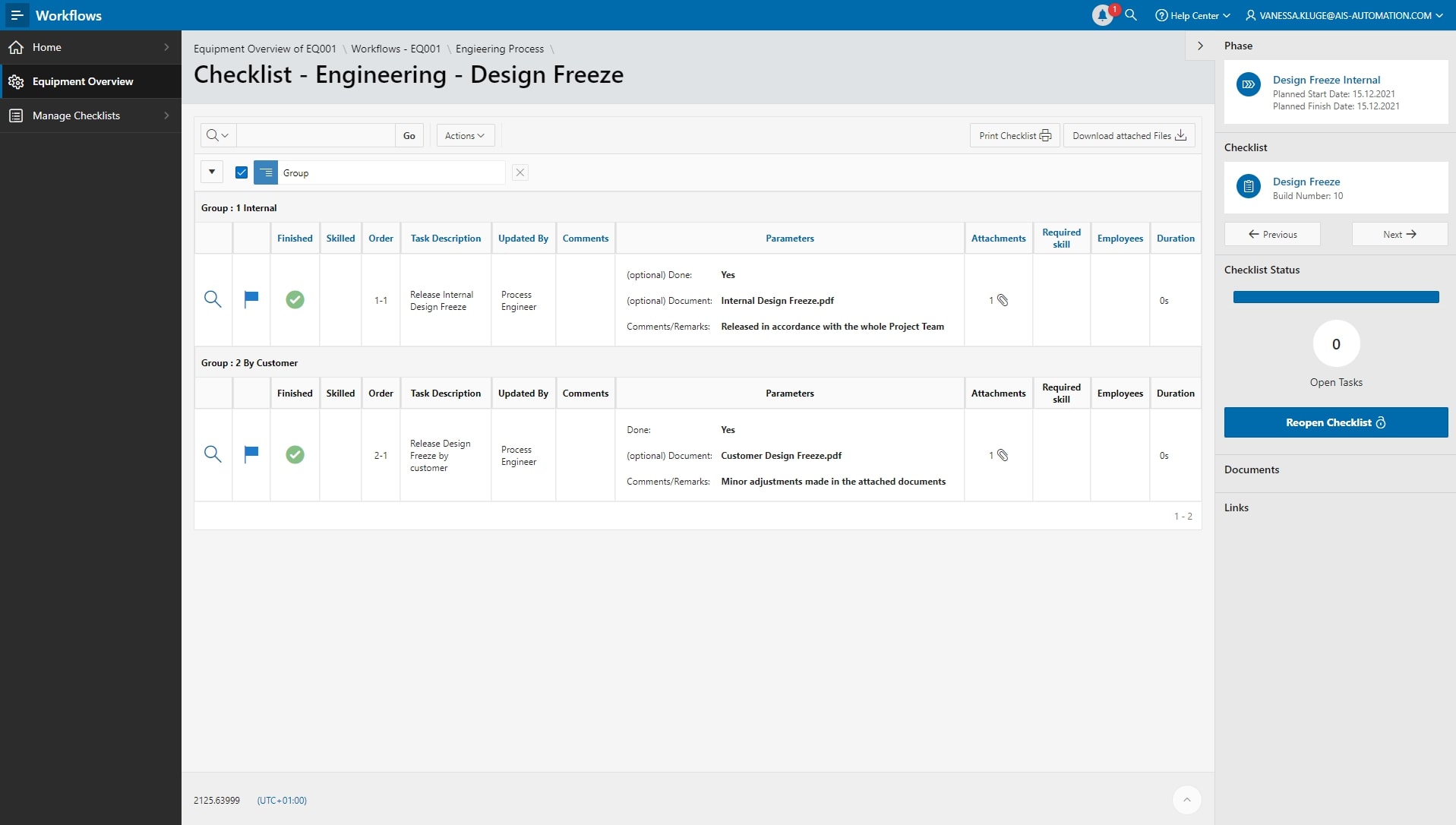
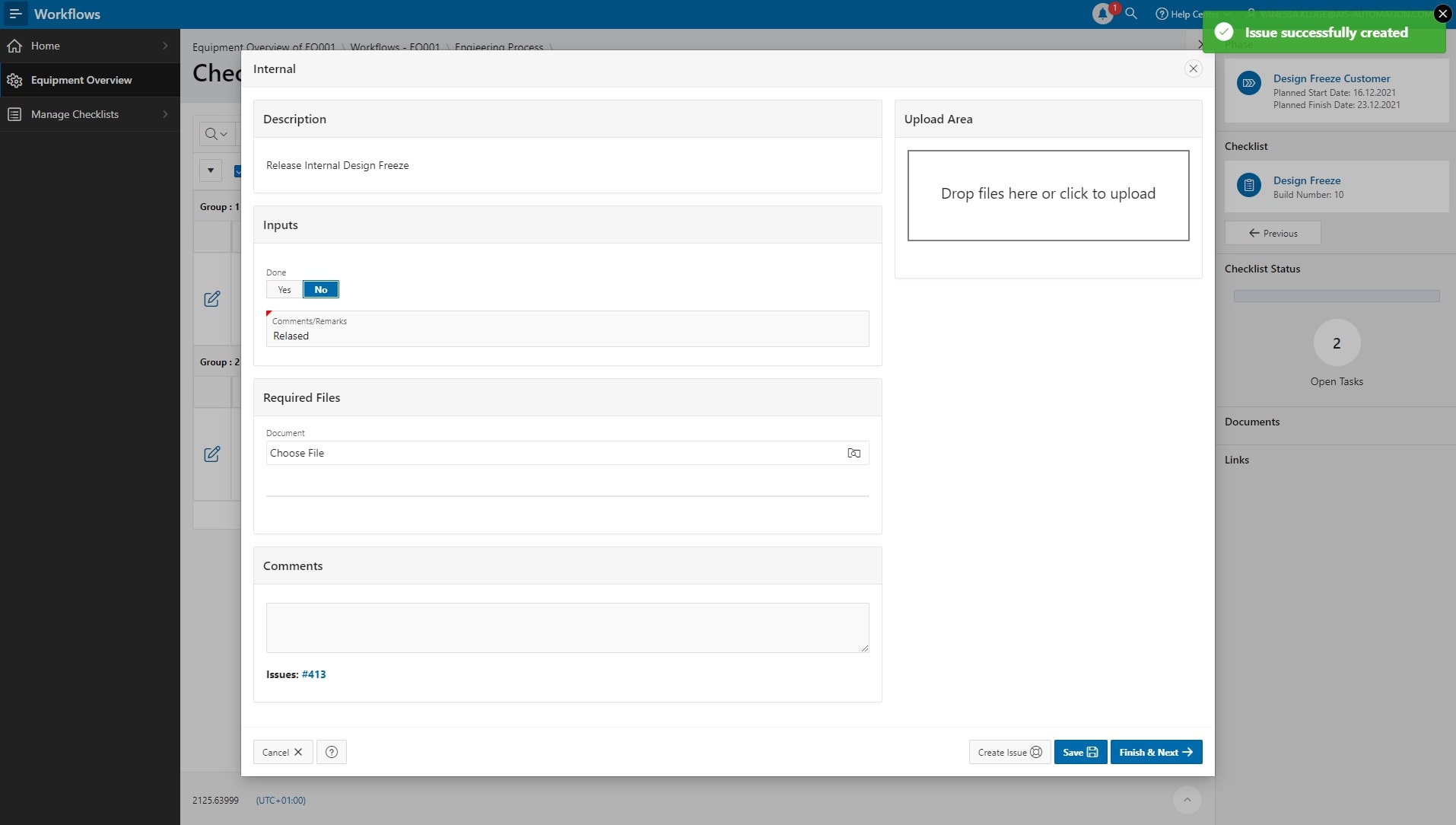
Checklist tasks can be worked through flexibly. The operator can proceed chronologically or can simply skip individual tasks or entire groups. Obligatory parameters must be filled in, otherwise the checklist cannot be completed successfully. This ensures that important steps are not forgotten during commissioning. It is also possible to upload files to the checklist for each task, such as images, screenshots and log files. If problems or issues that require clarification arise during the course of the project, an open task can be created directly in the OpenIssue module from the respective task in the Workflows module and passed on to the relevant departments and experts. A direct link is generated in both modules for easy navigation and as a reference.
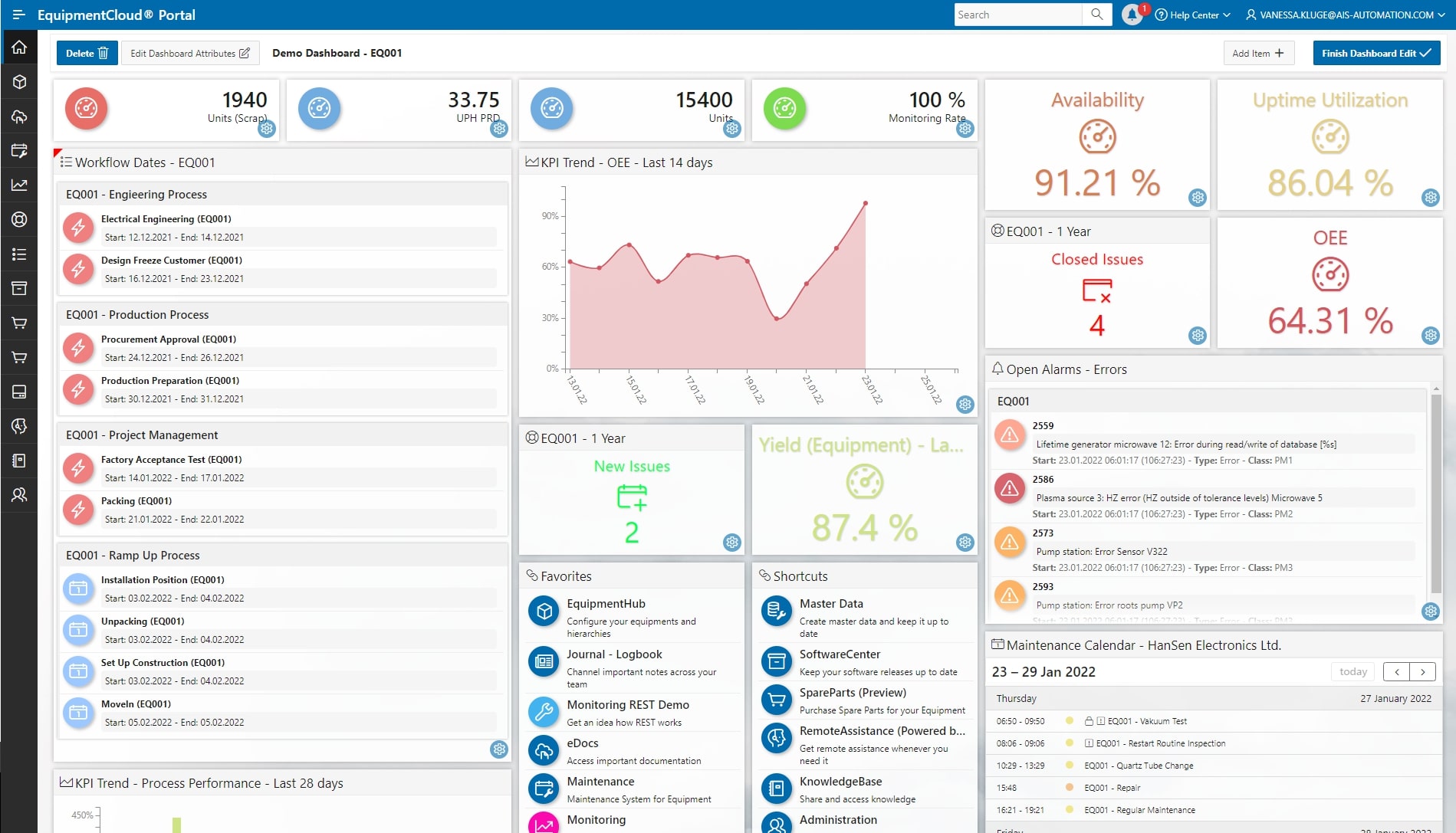
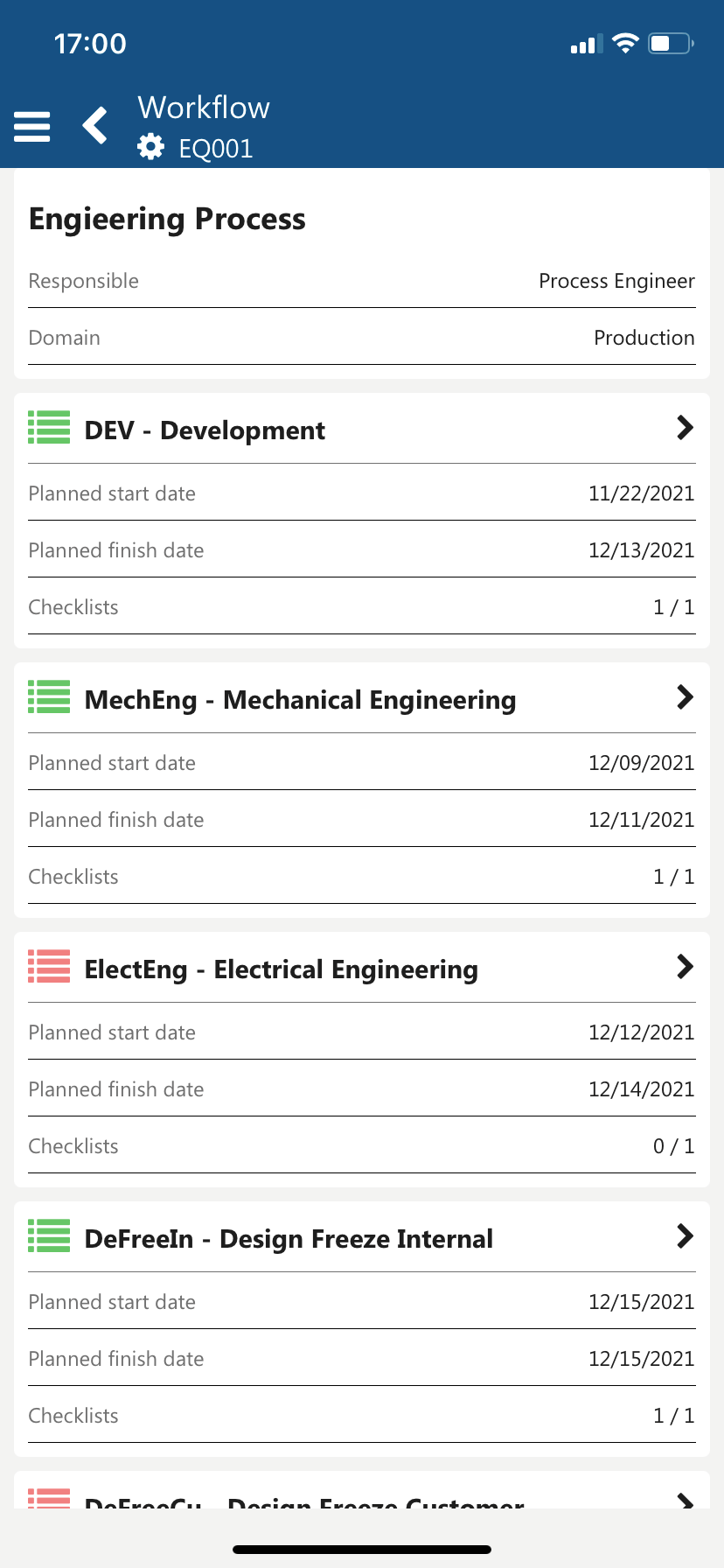
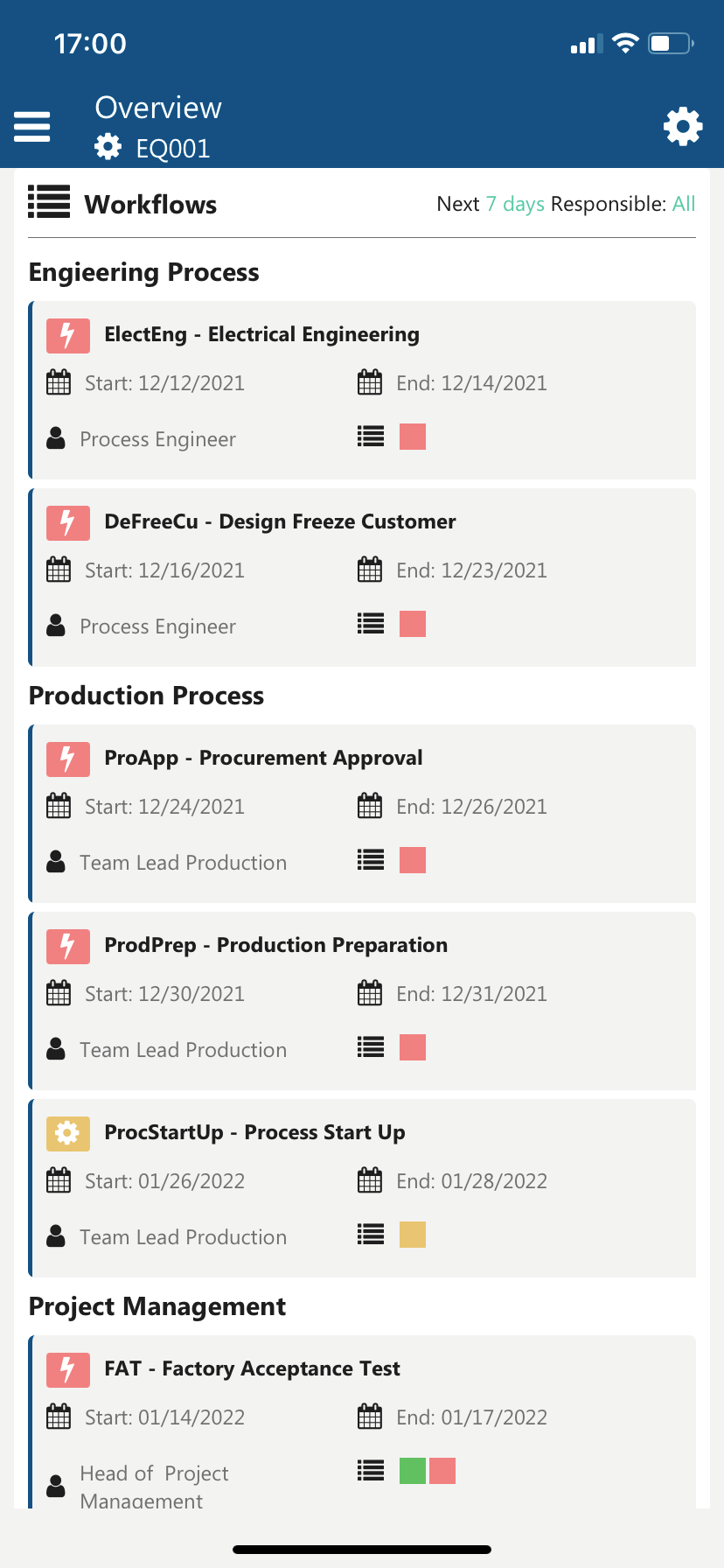
In addition, the dashboard item offers the possibility to set important milestones for workflow due dates directly on the digital workplace in the start screen of the customer and service portal. This ensures that project managers and service staff remain informed at any time and on a daily basis about open or upcoming due dates for single machines, whole plants or machines belonging to specific customers or regions. In the event of unexpected delay, this allows a quick response. For day-to-day project work, the tool is particularly suitable for proactive coordination of the team.
Ultimately, the Workflows module creates transparency and trust by allowing all team members to access the same data at any time, both internally and externally. Tasks can be assigned to people with the necessary skills. Registered tasks that have already been completed can no longer be changed. By recording the name, date and time, the process can be transparently proven in audits and shared with the customer. Dedicated visibility levels can also be defined for individual workflows, phases and checklists, which make it possible to determine with a high level of detail which content is visible to which stakeholders. This offers a completely new level of freedom to involve a wide range of project partners to different extents within a complex workflow.
The Workflows module is also an excellent basis for discussion at project meetings, because all the information such as status, progress, completed and open tasks, checklists and responsibilities is displayed in one place.
Do you recognize this scenario? Do you want to avoid unnecessary discussions and lengthy meetings with project participants? Are you looking for an intelligent tool to make your processes more efficient and faster? Then get to know the Workflows module as part of the EquipmentCloud® service and after-sales solution for a trial period of 30 days.