The hectic day-to-day service routine in mechanical engineering involves employees in service support, field service, maintenance and service management having to face the challenge of working according to clear strategies and structures. A great deal of experience and resilience are often required to maintain these over the long term. But what do you do when time is of the essence, resources are limited, and new team members need to be brought up to speed as soon as possible?
Continuous transfer of knowledge and proactive, efficient internal communication are the foundations of a successful service department. To ensure the efficiency and quality of the service provided, precise planning and a comprehensive overview of the team's tasks are required. That is why software integration is becoming an unavoidable necessity. What makes all the difference is when the tools used not only reflect existing service processes, but also take the pressure off running day-to-day operations without completely turning proven processes upside down. The challenge is to reduce worry and misconceptions that often accompany the introduction of new software solutions, while paving the way for positive change.
In this article, we present the often overlooked but decisive tools included in the EquipmentCloud® digital transformation solution for service and after-sales teams that make your everyday service routine easier, more effective and more efficient. From the smooth planning of service assignments to easily finding the information you need, and from retrieving recurring statistics to assistance with everyday tasks.
Get all the information you need and make it easy to find
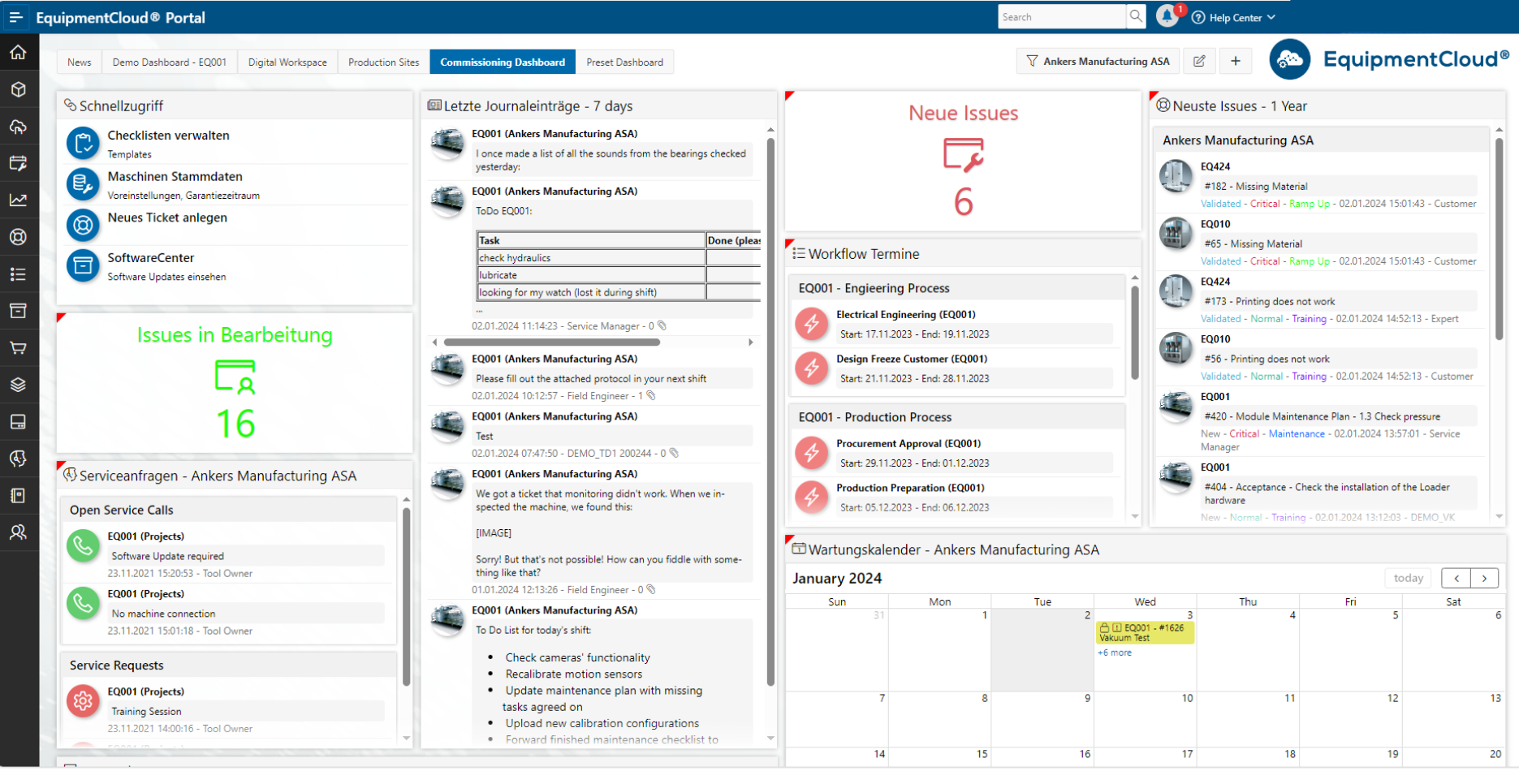
You know the situation: A complex schedule of machine maintenance is due, but the maintenance info and historical data relating to the machine are missing or difficult to find. Searching for the documents takes up precious time that should actually be spent on maintenance. You can change that with these life hacks:
1. Global search: Use this function to search the customer portal quickly and efficiently for various types of information (indexed documents, tickets, knowledgebase entries, master data). Access the search function directly from the sidebar in each module. It includes search filters for specific page areas in all modules.
2. Template snippets: Use these templates to easily structure all the information you get from service technicians and customers for logbook entries and pending tasks. This prevents delays in processing due to missing information.
3. User-related dynamic dashboards: Use these to present important information, key figures and developments in the form of lists, direct links, diagrams and maps for service and maintenance technicians, and service managers. Dashboards increase efficiency by making it easy to access information and process and prioritize daily tasks.
Display and share recurring and up-to-date information
Does your company have highly complex machines and systems that are used by customers all over the world? To ensure smooth operation and customer satisfaction, it is crucial to efficiently retrieve and share recurring information that is up-to-date. We have some tips for you on how you can use your data even more efficiently, increase your service success and improve communication both within your company, and with your customers.
4. Simple reporting and KPIs for service managers: Regular reports are essential for service managers to be able to evaluate important key figures such as response rate, tickets processed vs. pending tickets as well as completed maintenance orders and, as a result, make service success measurable. Two functions help here: Firstly, this information can be filtered by status, category and priority and saved as open reports. This has the advantage that only the time filter needs to be adjusted at the time of generating the report and then the report can be downloaded in various formats. And secondly, the figures can be directly visualized graphically in diagrams without having to take the detour via Excel.
5. Master data as a parameter in checklists: Master data relating to machines and systems changes over the course of the life cycle, such as measured values or configurations that need to be readjusted. Generally, these are adjusted during regular maintenance jobs or as part of an upgrade or retrofit so that it is possible both to understand how these measured values have changed and at the same time ensure that this is recorded centrally in the machine’s logbook. So the life hack here is, instead of making separate entries, service technicians can directly enter the master data as a parameter in the digital checklist when carrying out the maintenance order. The logbook is automatically updated with details of when, by whom and where the change was made to ensure that the current configuration is immediately visible to all stakeholders.
6. Global notifications: Use this function to centrally communicate important innovations on machines and systems as well as upcoming software updates that affect a wide range of customers. The global notification function makes it possible to inform users throughout the entire customer portal, or users within a specific target group, by email and, when logging into the portal, with a visual notification for a defined period of time. The target group can be defined very narrowly according to user domains.
7. Permalinks: To make it easier to access relevant information, permanent links are provided that don't change and can be integrated into messages, emails, or posts. These take users directly to the information they need in the service and customer portal.
8. Detailed factory view of individual locations: The fabrication view or FabView has the advantage over the map view that the plants and machines can be visualized within a location using SVG geolocation files. Users can choose between different hierarchical levels (individual machines, a work area or even an entire factory location). In addition, areas within the map can be defined which highlight the current machine status (productive, unplanned downtime, etc.) in real time in order to provide service technicians with a quick overview.
9. Embed HTML web pages: When launching a customer portal, most mechanical engineering companies don't start from scratch. Existing information such as parts lists and spare parts lists in HTML format can be integrated directly into the customer portal. This makes integration into existing work processes easier and bundles all the relevant information in one place.
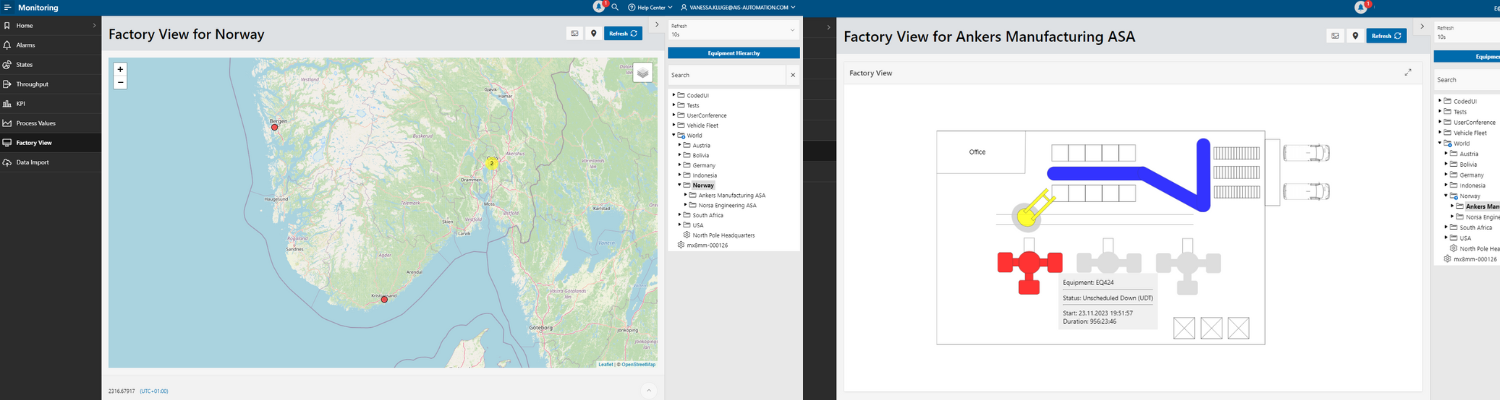
Efficient and structured planning
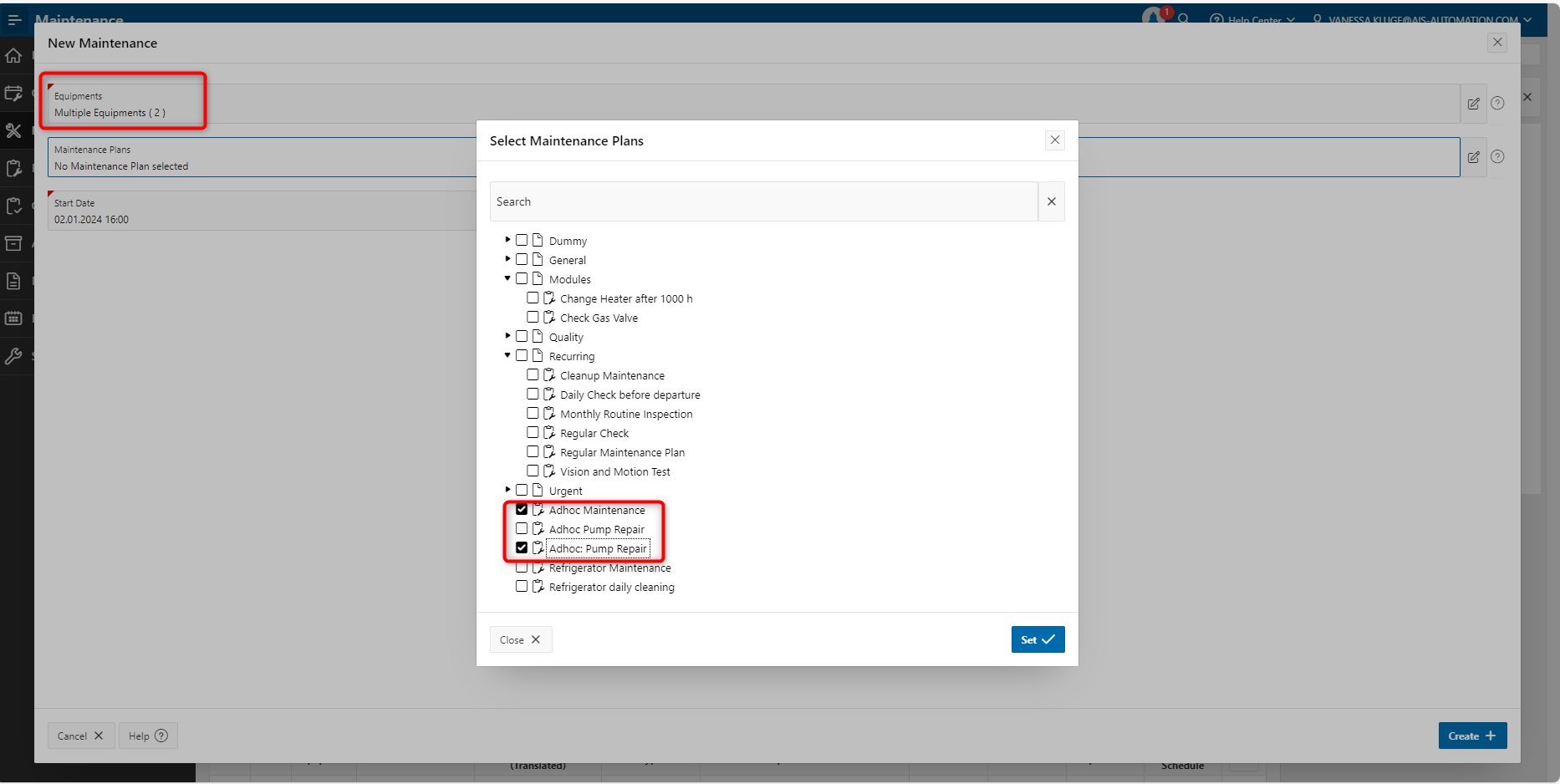
Efficient and structured planning processes are crucial for successful service and after-sales support. Customers not only expect high-quality machines, but also reliable and timely assistance. Maintenance work is often complex and the workload of technical staff is high. The following tips will help you save time and work more efficiently.
10. Creating maintenance orders: This process should be as easy as possible for service managers. Scheduled maintenance during the warranty period is often mandatory and only differs slightly from machine to machine. Here, checklists containing tasks can be created as templates and assigned to maintenance plans, which can then be selected when creating maintenance orders. These can be assigned not only to individual machines, but also to multiple machines and machine types. This makes maintenance order planning particularly efficient.
11. Modules within checklists: Using modules within checklists ensures that when carrying out maintenance, service technicians are only shown the tasks that are relevant to the respective module. This means that templates can be planned to cover everything, but then fine-tuned to the essentials for each maintenance order. This saves time both during planning and during implementation.
12. Calendars: These are the most common tools when it comes to scheduling appointments, and can be used on a smartphone, tablet or laptop. The pre-filtered maintenance calendar can be exported as a CSV file and manually stored in the relevant calendar so that the service technician always has their assignments at hand. It is even easier to check out upcoming maintenance in the EquipmentCloud® mobile app, which will remind service technicians in good time by push notification.
13. Time limit for news posts: Upgrades, new service offers or news about machines are usually only up to date within a certain time limit. The time limit can be set as soon as the news posts are created. This saves effort and ensures that customers always receive relevant information.
Quick system-assisted work steps
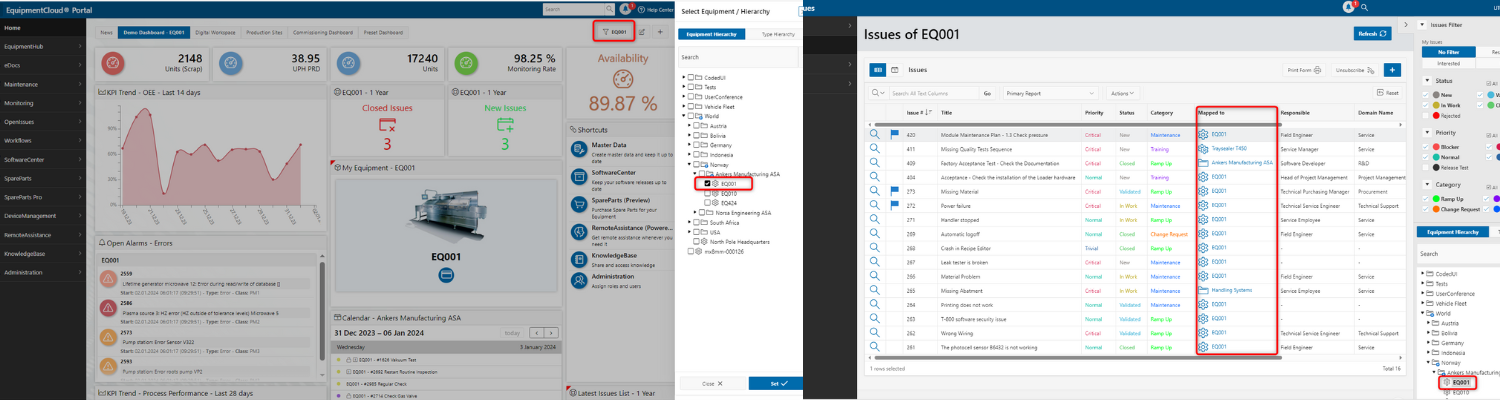
With these work steps, you can complete routine tasks faster and more precisely:
14. Confirm deletion by right clicking and copy-and-paste: To prevent data from being deleted unintentionally, only certain users are authorized to actually do so. However, before they irrevocably delete journal entries, comments, documents, etc., the process must be confirmed. To avoid having to do this manually, there is a clever copy-and-paste function that can be carried out with a right click.
15. Memory function: The equipment filter, which is available both in the dashboard and in all modules, is essential for giving service managers and service technicians a comprehensive overview of the life cycle of the machine. So that the information does not have to be re-filtered on every page, a memory function is available, which is activated as soon as the equipment filter is used. This means that service technicians can easily jump from master data to open tasks, or from alarms to status data.
16. Hover in the dashboard widget: The dashboard helps the service team get an intuitive and fast overview of important developments, events and data. In certain situations, it is better to use the data displayed on the dashboard widgets, rather than diving straight into the detail in each module. The hover function can be used for this purpose, allowing you to zoom in on work overviews or diagrams.
17. Transfer ad hoc process value correlations into saved profiles: Service technicians are repeatedly confronted with service requests that require in-depth data analysis. Process values such as pressure, temperature, humidity and speed can provide important information about sources of error here. In the monitoring module, the required process values can be correlated and evaluated using various statistical tools. Especially with regard to long-term analyses, it makes sense to carry this out on a permanent basis. Ad hoc correlations can be converted into saved profiles with just a few clicks, which can later be retrieved by clicking on a tab and can also be made available to the entire service team, or as an open report to the customer.
18. Copying dashboard widgets: For service technicians who are responsible for specific customers or machine types, it is helpful if widgets contain pertinent information and data that can be directly compared with each other without having to adjust the equipment filter. When creating or customizing the dashboard, service technicians save a lot of time thanks to the widget's copy function.
Admin made easy
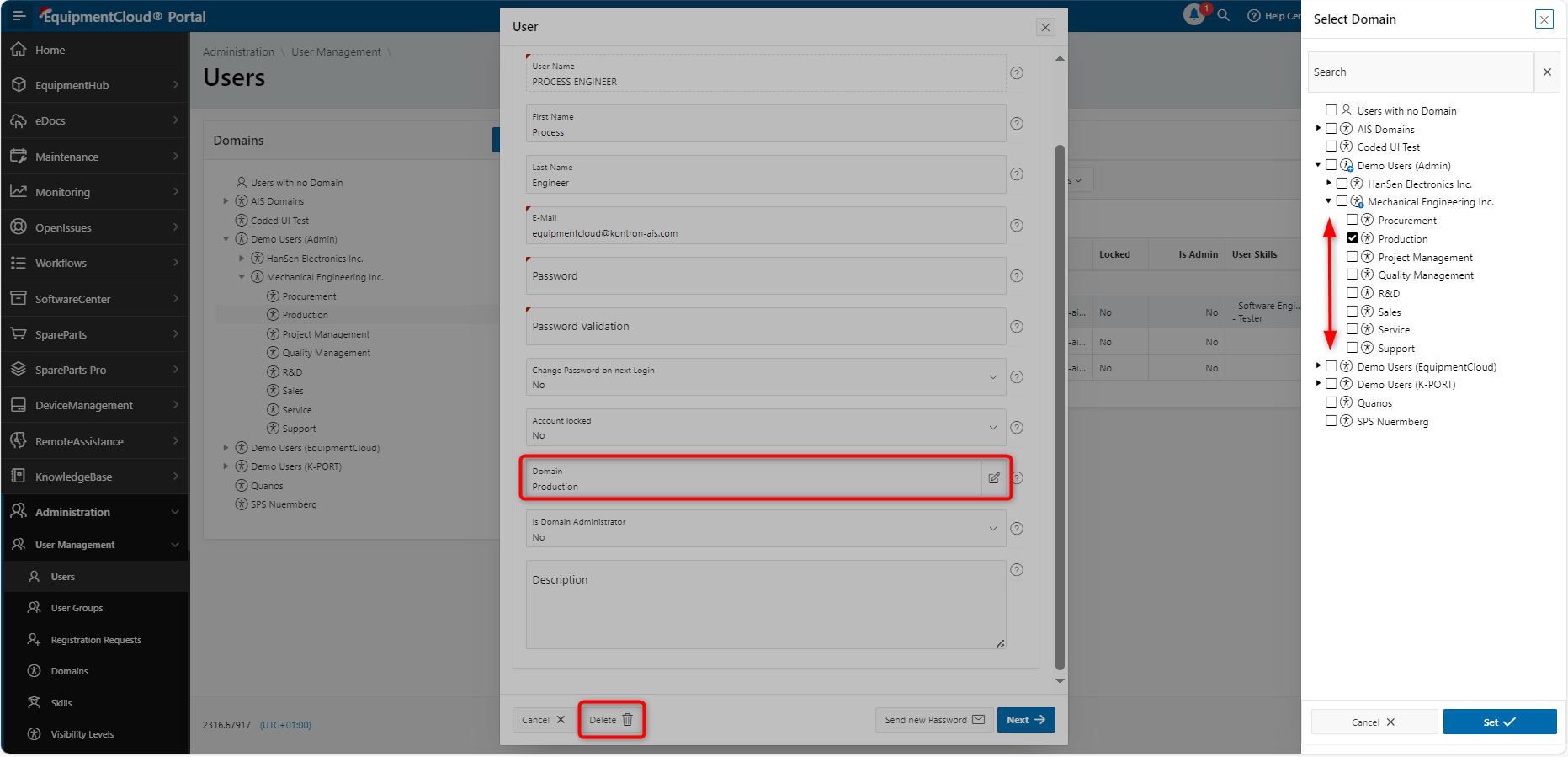
Customer portals are increasingly becoming the hubs of modern digital services. The administration of your customer portal should be as simple and intuitive as possible. Have you checked out these functions?
19. Default visibility level for all modules: The administration of a customer portal needs to be systematic and structured so that the information reaches the right people (company employees, customers, general open report recipients). Manual settings do not make sense here, which is why administrators can set the visibility levels by default for all modules in one place and decide whether the content is linked to the users' visibility levels or should be displayed openly. Once they have been determined, these settings are automatically adopted for all other users. This simply saves you time.
20. Easy assignment, movement and deletion of users: In view of high employee turnover and regular changes of functions and teams, it is all the more important for service managers to be able to easily delete users or move them to other functional areas or user groups. The same applies to adding competencies following successful completion of courses and qualifications. This has the advantage that service managers always know who has which competence profile and can draw on a larger or more up-to-date number of employees while identifying gaps in the personnel spectrum.
21. Activate service package-based content: Service is increasingly becoming a revenue driver in the mechanical engineering sector. By setting up a customer portal and recording and visualizing machine data, the next logical step is to put together various paid service packages that offer operators new added value based on data and in-depth information. In order to activate this content for the customer depending on the service package they have ordered, service and after-sales managers can individually activate or deactivate sub-menus such as KPIs, status, throughput, etc.
Helping people to solve issues themselves
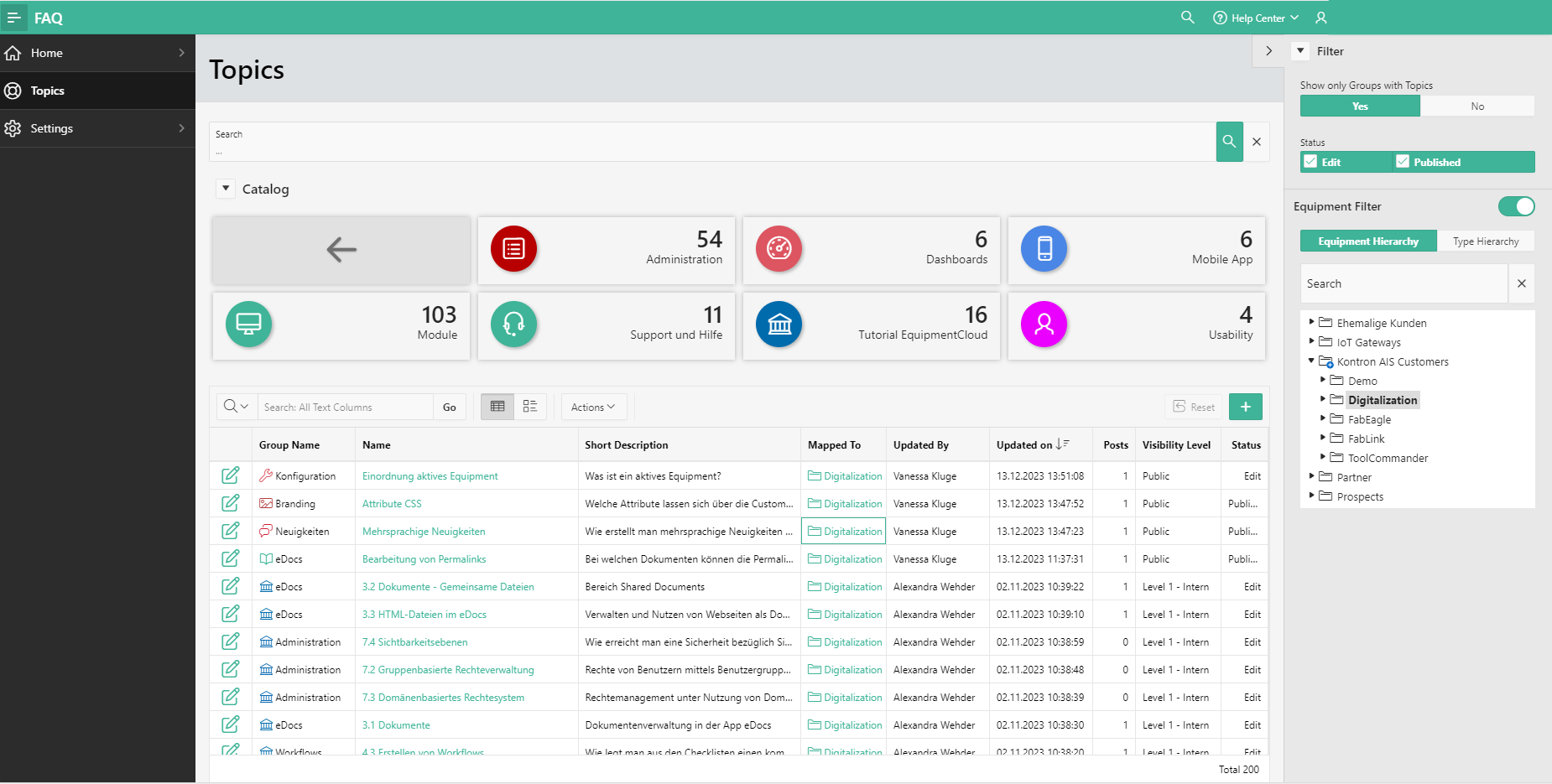
Any more questions? Sometimes, in-depth background knowledge and easily accessible assistance are essential. All the better when they are available in one place and at any time to save having to carry out a long search and to be able to provide answers quickly.
22. Background knowledge: If questions arise about administration, particularly during the onboarding process or during the follow-up introduction of new modules, it is particularly helpful for administrators to be able to draw on in-depth background information, practical examples and short tutorials. For this purpose, extensive documentation has been created, which is constantly being expanded and can be accessed at any time using the Help Center.
23. FAQs in the customer portal: Service managers and service technicians are more and more likely to be confronted with ad hoc questions about how to use the constantly growing range of functions of EquipmentCloud®. That is why we have built a knowledge database in the Kontron AIS customer portal that answers frequently asked questions and shows various solutions. It's worth taking a look!
Service managers and technicians are often under tremendous pressure to provide high-quality, customer-focused service, while dealing with a shortage of resources under time pressure. That is why it is high time to relieve them of their workload over the long term so that they can concentrate on their actual job of providing high-quality and customer-driven service.
The tools in the EquipmentCloud® digital transformation solution mentioned above ensure the efficiency, responsiveness and effectiveness that service and after-sales teams deserve in order to provide the best quality of work possible.
Are you also struggling with time pressure and resource problems in your service department? Book a consultation now to find out how you can elevate your service to the next level.