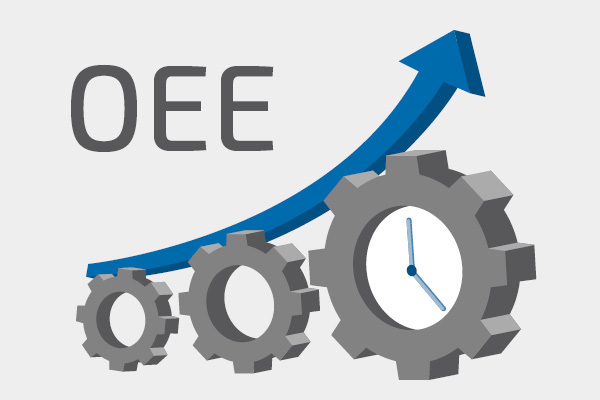
Keine OEE ist wie die andere! Wie sich Maschinen übergreifend auswerten lassen
Der goldene Standard OEE – was steckt dahinter?
Der goldene Standard OEE (Overall Equipment Efficiency), auch Gesamtanlageneffektivität genannt, ist mitunter DER Fertigungsstandard, um die Produktivität von Anlagen, Prozessen und Geräten zu messen. Die Kennzahl (KPI = Key Performance Indikator) OEE ist für das Produktionscontrolling ausschlaggebend, da sie es ermöglicht die Performance von Anlagen unter Einbezug der Einflussfaktoren Verfügbarkeit, Qualität und Leistungsgrad zu ermitteln. Das heißt die OEE gibt Feedback zur Produktivität über einen bestimmten Zeitraum und die Einflussfaktoren geben Aufschluss darüber, wo Verbesserungen anzusetzen sind.
- Verfügbarkeit: Anteil der Gesamtzeit, in der die Maschine für die Produktion zur Verfügung steht. Dieser Faktor berücksichtigt alle Stillstandszeiten – geplante wie ungeplante Stillstände, Störungen, Produktionspausen und andere Ursachen.
- Qualität: Ermittlung der produzierten Gutteile im ersten Durchlauf, die keine Nacharbeit mit Mehraufwand erfordern oder die nicht als Schlechteile ausgeschlossen werden müssen.
- Leistung: Geschwindigkeit oder Zykluszeit mit der die Maschine betrieben wird. Kurzstillstände und langsame Zykluszeiten werden mit einberechnet. Maschinenverschleiß, minderwertige Materialien, Fehleinzüge oder Staus beeinflussen die Leistung. Voraussetzung für die korrekte Berechnung ist eine genaue Ermittlung der Zykluszeit.
Wie Echtzeit-Daten die Produktivität nachhaltig steigern
Maschinendaten in Echtzeit zu erfassen, zu kontextualisieren und die OEE automatisiert zu berechnen hat gegenüber der manuellen Erfassung durch den Bediener folgende Vorteile:
- Geringere Fehleranfälligkeit und höhere Genauigkeit
- Zuverlässige und kosteneffiziente Erfassung
- Unmittelbare Weiterverarbeitung der Daten für die Korrelation und Analyse sowie Ableitung von Optimierungsmaßnahmen
- Steigende Produktivität durch gewonnene Zeitersparnis und sichtbare Verantwortung
OEE-Kennzahlen richtig einordnen
Die Multiplikation der drei Einflussfaktoren Verfügbarkeit x Qualität x Geschwindigkeit ergibt die Gesamtanlageneffektivität (OEE).
- 100 % – Der Idealzustand. Die Produktion läuft perfekt, weist keinerlei Ausfallzeiten auf und Produkte höchster Qualität produziert.
- 85 % – Ein Weltklasse-Wert. Er wird von vielen Herstellern langfristig für die Produktion angestrebt. Werte, die darüber liegen, lassen häufig geplante Stillstandzeiten außen vor.
- 60 % – Der faire Wert. Die Produktion hat Verbesserungspotential.
- 40 % – Für Anfänger und Durchstarter. Verbreitetes Produktivitätslevel von Unternehmen, die bisher keine OEE erfassen oder gerade erst damit beginnen.
Was die Gesamtanlageneffektivität leisten kann und wo ihre Grenzen sind
Die Relevanz der OEE ist unbestritten. Vergleiche sind dann sinnvoll, wenn es sich um Anlagen und Maschinen des gleichen Typs handelt. Zudem muss das gleiche Produkt unter demselben Produktionsprozess hergestellt werden. Zu kurze Betrachtungszeiträume z.B. auf Stunden-, Tages- oder Schichtbasis können die Aussagekraft der OEE schmälern oder gar verzerren, da Produktionsspitzen oder Ausfälle eine zu hohe Gewichtung erhalten und für den Zeitraum nicht ausreichend Daten gesammelt wurden. Längere Zeiträume auf Monats- oder Quartalsbasis sorgen für den glättenden Ausgleich und geben eine aussagekräftige Datenbasis für die Ermittlung der Produktionskennzahl OEE und der Identifikation der damit zusammenhängenden Verbesserungspotentiale. Genau hier liegt aber die Krux der Kennzahl. Sie beschreibt, was über einen Zeitraum passiert, und ist daher eine reine Momentaufnahme. Die OEE sollte daher nicht allein betrachtet werden, denn nur im Zusammenspiel mit den Einflussfaktoren Qualität, Leistung und Verfügbarkeit kann ermittelt werden, wo die Ursachen für die existierenden Schwachstellen liegen. Ebenso lassen sich Maßnahmen besser greifen und einzelne Parameter ändern und deren Auswirkungen ganzheitlich einordnen.
Obwohl viele Produktionsprozesse heutzutage vollautomatisiert sind, gibt es immer wieder Teilprozesse, die manuell durch Bediener, Werker oder auch Tool Owner durchgeführt werden und die automatisierten Abschnitte aus Sicherheits- oder Komplexitätsgründen flankieren. Hier sollten aber keine Blindspots entstehen, sondern es bedarf einer vollständigen Erfassung des gesamten Produktionsprozesses. Abhilfe können dabei sogenannte Werkerterminals leisten, mit denen der Status der Anlage, Alarme oder auch Durchsätze manuell digital erfasst werden können. Darüber hinaus verfügt dieses Fachpersonal in der Regel über ein ausgeprägtes Anlagenverständnis, das so weit reicht, dass sie abweichendes Verhalten hören oder sogar „spüren“ können. Dieses Domainwissen ist für die Umsetzung von Verbesserungsmaßnamen essenziell. Eine zeitige Einbindung des gesamten Produktionsteams, bereits bei der Datenerfassung, ist daher für eine erfolgreiche Implementierung entscheidend. Denn das Engagement steht und fällt mit der Motivation aller Beteiligten. Außerdem lassen sich Optimierungsmaßnahmen und gewünschte Ziele durch aktive Teilhabe an der Problemlösung durch funktionsübergreifende Teams und deren diverses Know-how effizienter und wirkungsvoller erreichen.
Darum ist der Wunsch der Maschinen- und Anlagenbauer nach einer individuellen OEE sinnvoll
In der Betriebswirtschaftslehre wird davor gewarnt Äpfel mit Birnen zu vergleichen, auch im Zusammenhang mit der OEE ist dies mit Vorsicht zu genießen. Trotz der verbreiteten Anwendung der Kennzahl, ist davon abzuraten dieselbe OEE-Berechnung anlagen-, standort- oder industrieübergreifend anzuwenden. Warum? Weil die Rahmenbedingungen und Voraussetzungen des Produktionsprozesses von Anlage zu Anlage, von Standort zu Standort sowie von Industrie zu Industrie im Maschinen- und Anlagenbau nicht unterschiedlicher sein können. Hier sind stattdessen viel Erfahrung und eine individuelle Ausrichtung der Kennzahlen für jedes Unternehmen gefragt. Was aber gleichzeitig nicht bedeutet, die OEE für das Management zu beschönigen, da diese statt den realistischen 85 % lieber 100 % sehen würden, sondern den Fokus weiterhin auf die Indikation von Potentialen zu legen.
Branchenspezifische Kennzahlen – ein Ansatz
Eine Möglichkeit nicht völlig bei null zu starten, ist der Einsatz von branchenspezifischen Kennzahl-Modellen. Zwei gängige KPI-Modelle sind die SEMI E10 Norm für die Halbleiterindustrie und die VDI 3423 Richtlinie für den Maschinen- und Anlagenbau. Deren OEE-Berechnung berücksichtigen spezifische Maschinenzustände und nutzt andere KPI-Begrifflichkeiten.
SEMI E10 Norm: Die SEMI E10 Norm, spezifiziert die Definition und Messung der Zuverlässigkeit, Erreichbarkeit und Wartbarkeit von Geräten (RAM). Die Norm definiert sechs verschiedene Maschinenzustände: Productive Time, Standby Time, Engineering Time, Scheduled Time, Unscheduled Time, Non-Scheduled Time.
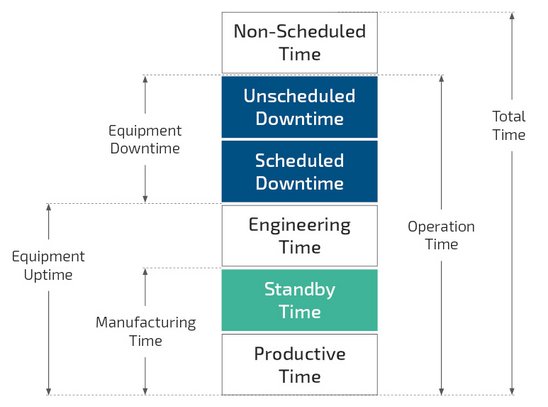
So setzt sich die OEE-Berechnung nach SEMI E10 aus den folgenden Faktoren zusammen:
OEE = Verfügbarkeit (AV) x Nutzungsgrad (UU) x Prozessleistung (PP) x Ausbeute (YLD)
Die eingangs beschriebenen Begriffe werden nachfolgend noch einmal erläutert und um den Nutzungsgrad ergänzt:
- Verfügbarkeit (AV): Die Verfügbarkeit zeigt an, wie gut der Wartungszustand und die Zuverlässigkeit der Maschine ist. Durch das Verhältnis von Zeit, die für die Produktion nutzbar ist, zur Gesamtzeit, werden die Zustände geplante Stillstandzeit (SDT) und ungeplante Stillstandzeit (UDT) bewertet. Je besser das Wartungsteam die Maschine pflegt und diese Aufgaben optimiert, umso höher ist die AV.
- Nutzungsgrad (UU): Der Nutzungsgrad bewertet die tatsächlich zur Produktion genutzte Zeit mit der gesamt nutzbaren Zeit. Damit wird bestimmt, wie gut die Produktion organisiert ist, unter Berücksichtigung von Standby und Engineering Zeiten. Der UU ist umso besser, je mehr Zeit auch tatsächlich in die Produktion eingebracht wird. Logistische Probleme wie Materialzuführung und Verfügbarkeit von Bedienpersonal führen zur Absenkung des Nutzungsgrads.
- Prozessleistung (PP): Die Prozessleistung bestimmt die Geschwindigkeit der Maschine, in dem die erreichte Stückzahl mit der theoretisch möglichen Stückzahl ins Verhältnis gesetzt wird. Je schneller die Maschine produziert, umso höher ist die PP. Ein Wert von größer 100 % ist dabei nicht möglich, da höchstens die theoretisch maximale Geschwindigkeit zu erreichen ist.
- Ausbeute (YLD): Die Ausbeute definiert das Verhältnis von verkaufbaren (guten) Teilen zu allen hergestellten Teilen und ist somit ein Ausdruck der erreichten Produktqualität. Wenn kein Ausschuss produziert wird, kann der YLD maximal 100 % erreichen.
VDI 3423 Richtline: Die VDI 3423 Richtlinie ist vom Verein Deutscher Ingenieure definiert. Dieses Modell bewertet Maschinen unter den Blickwinkeln der Produktion sowie der dort organisierten Verantwortlichkeiten. Die Standardisierung erlaubt einen Vergleich von sehr unterschiedlichen Anlagen in Bezug auf Wirtschaftlichkeit, Garantieansprüchen oder zur Unterstützung von Investitionsentscheidungen. Die Richtlinie unterscheidet zwischen Einzelmaschinen und Komponenten und berücksichtig die fünf Maschinenzustände Utilisation Time, Organisational Time, Technical Downtime, Maintenance Time und Test Time
Bei der VDI 3423 Richtlinie beeinflussen folgende Kenngrößen die OEE:
- Die Belegungszeit TB ist die Zeit, die für die Maschine eingeplant ist. Sie bildet die Bezugszeit für weitere Kenngrößen des Standards.
- Die organisatorische Ausfallrate AO gibt die Ausfallrate infolge organisatorischer Mängel bezogen auf die Belegungszeit an.
- Die technische Ausfallrate TT gibt die Ausfallrate infolge technischer Mängel bezogen auf die Belegungszeit an.Die wartungsbedingte Ausfallrate AW gibt die Ausfallrate infolge geplanter Wartungsmaßnahmen an.
- Der Nutzungsgrad NG gibt das Verhältnis von genutzter Zeit für die Produktion im Verhältnis zur Belegungszeit an und ist damit ein Maß für die Effektivität.
- Die technische Verfügbarkeit VT gibt den Anteil der Belegungszeit an, für den die Maschine ohne technische Mängel der Produktion zur Verfügung stand.
Reichen die normale OEE-Kennzahl oder auch diese branchenspezifischen Standards nicht aus oder besteht der Wunsch nach individuellen Kennwerten, könnten dynamische KPI die passende Antwort sein.
Mit dynamischen KPIs auf maximale Flexibilität und hohe Vergleichbarkeit setzen
Dynamische KPIs sind sowohl für Maschinenhersteller von Relevanz, die unterschiedliche Maschinen und Anlagen im Sortiment haben, die sich nicht nach einheitlichen KPI-Modellen auswerten lassen als auch Betreiber, die ihre Produktion nach spezifischen Kennzahlen auswerten möchten. Zugleich möchte der Hersteller aber jederzeit die Möglichkeit behalten Maschinen eines Typs, eines Kunden oder einer Region weiterhin vergleichen zu können und hier auch zwischen unterschiedlichen KPI-Modellen, ergo OEE-Berechnungen flexibel wechseln zu können.

In der Digitalisierungslösung EquipmentCloud® wurde dafür im Monitoring Modul ein Formeleditor implementiert, der es zum einen ermöglicht die branchenspezifischen KPI als Vorlagen zu nutzen, zum anderen aber auch eigene Modelle festzulegen und einzelnen oder mehreren Maschinen zuzuweisen.
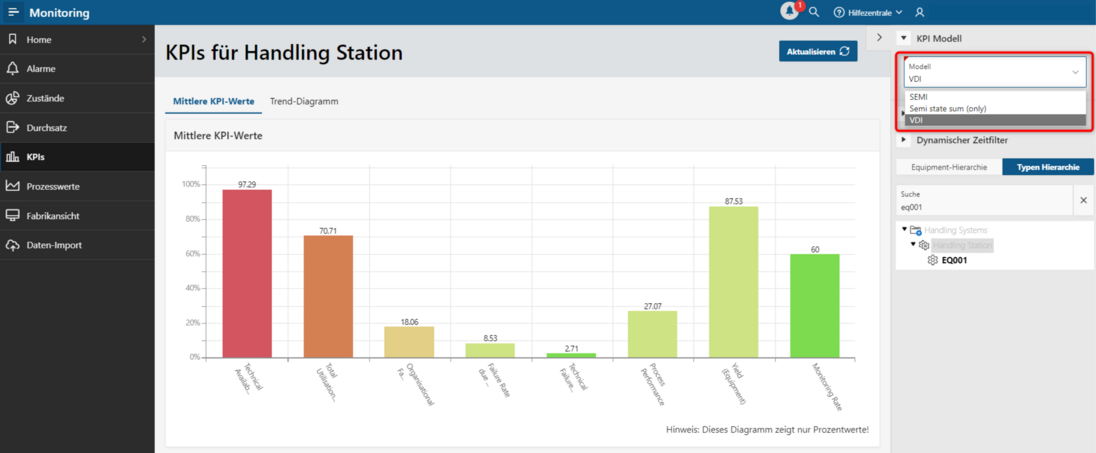
Ein praktisches Dropdown-Menü in der KPI-Ansicht ermöglicht dem Nutzer ein schnelles Wechseln zwischen den KPI-Modellen und eröffnet gleichzeitig übergreifende Maschinenvergleiche.
Sind Sie neugierig geworden? Dann vereinbaren Sie jetzt einen Demotermin mit unseren Expert*innen, um mehr für über dynamischen KPIs zu erfahren und wie sie in Echtzeit die OEE signifikant verbessern.
Sind Sie bereit, Ihre Digitalisierungsstrategie in der Praxis umzusetzen?
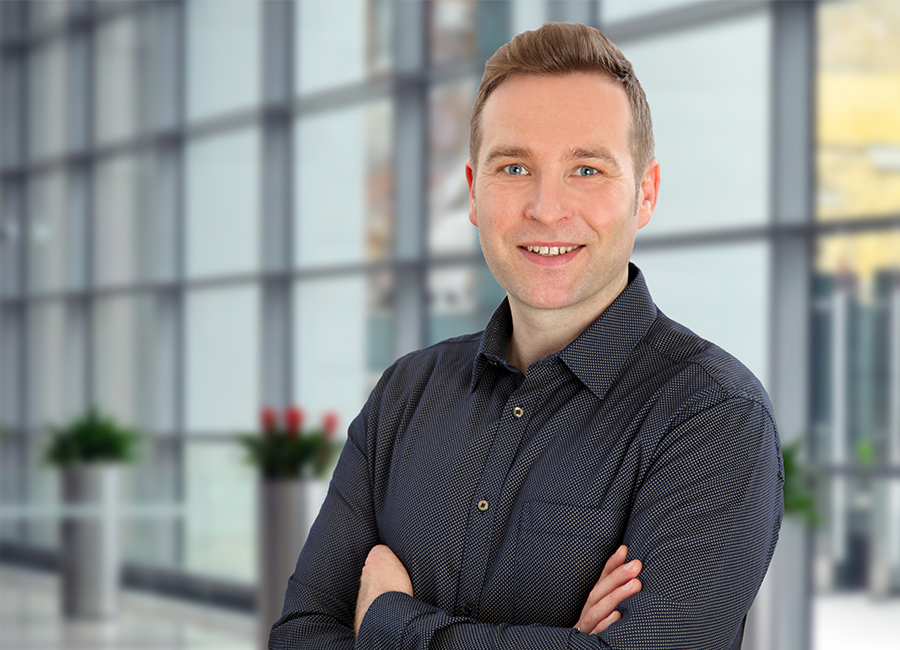