Corona-Zeit. Die Welt ist im Homeoffice. Die Wenigen, die auf Arbeit kommen, damit die Produktion weiterlaufen kann, folgen einem Zeitregime, das persönliche Begegnungen möglichst verhindern soll. Reisen von Servicetechnikern zu Betreibern von Maschinen und Anlagen stehen derzeit ganz oben auf der Not-to-do-Liste.
Trotzdem dürfen Wartungen von Maschinen auf keinen Fall aussetzen
Damit ist die große Zeit der Fernüberwachung angebrochen, der Remote Service. Das Internet ist plötzlich voll von einschlägigen Angeboten. Vergleichbarkeit? Fehlanzeige. Von den beiden wichtigsten Dingen reden die wenigsten. Das eine ist die Möglichkeit, auch in das Innere der Maschine sehen zu können, d.h. Fehlerquellen identifizieren, einordnen und direkt beheben. Das andere ist die Sicherheit der Daten. Natürlich geht es zumeist um cloudbasierte Tools. Aber von welcher Cloud-Architektur ist da die Rede?
Jetzt an die Digitalisierung im Maschinenbau denken
Nutzen wir die Ruhe zum Nachdenken. Hoffentlich nie mehr werden wir dafür so viel Zeit haben wie jetzt. Aber so hat es auch etwas Gutes. Wollen wir wirklich nur über eine kurzfristige Lösung für das aktuelle Problem des Remote Service für unsere Kunden nachdenken – um nach der Krise feststellen zu müssen, dass wir zu kurz gedacht haben? Gute Remote-Lösungen sind das eine. Die große Digitalisierungslösung, die ohnehin an die Tür klopft, und zu der Fernüberwachung zwingend gehört, ist das andere. Jetzt ist die ideale Zeit, die Digitalisierungsstrategie für den Maschinenbau in die Wege zu leiten.
Es geht um die umfassende Datenintegration
Die mangelnde Verwaltung der Maschinendaten ist eines der größten Hemmnisse für die Digitalisierung. Denn meist sorgen Schnittstellenvielfalt und Inkompatibilität der Anlagen untereinander für Schwierigkeiten. Insellösungen sind gerade im mittelständischen Maschinenbau verbreitet, denn Flexibilität wird hier großgeschrieben. Diese Insellösungen werden zur Lösung eines spezifischen Problem eingesetzt, aber das Zusammenwirken über Abteilungsgrenzen hinweg oder zu angrenzenden Systemen bleibt hier häufig unberücksichtigt.
Eine Stufe tiefer setzen sich die Probleme fort. Auch einzelne Maschinen produzieren heute vor allem eines: Daten. Wenn man sie gut verwaltet und geschickt nutzt, können sie Wunder an Effizienz und Laufsicherheit bewirken. Nachlässigkeit hingegen stiftet heute Chaos. Benötigt wird ein Instrument zur umfassenden Integration der Daten aller im Einsatz befindlichen Maschinen. Ein Teil davon wird anfangs gar nicht aktiv genutzt. Er gehört ins virtuelle Archiv, wo er zum Grundstock für die digitale Zukunft, also für Künstliche Intelligenz und Industrie 4.0, wird. Aber es gibt genügend Maschinendaten, die heute schon gebraucht werden und die es professionell zu managen gilt, wie beispielsweise für folgende Nutzungsszenarien:
- Für die Inbetriebnahme (SAT, FAT) von neuen Maschinen und Anlagen
- Für die laufende Überwachung der Workflows
- Zur Dokumentenverwaltung aller zur Maschine gehörenden Handbücher, Anleitungen, Checklisten, Zertifikate, u.v.m.
- Zum Aufbau einer vorausschauenden Wartung (Predictive Maintenance)
- Für den Remote Service der Anlagen im Feld und
- Für das Ersatzteilmanagement
Hierfür braucht es außerdem Tools, welche die Datenbibliothek unter den genannten Aspekten gezielt anzapfen und die Daten gebrauchsfertig bereitstellen – für Instandhalter einer Anlage, Serviceleiter und Servicetechniker des Herstellers.
Durch Digitalisierung neue lukrative Geschäftsmodelle entwickeln
Es ist auch die Rede davon, dass man als Maschinenbauer die Last der Daten in eine Lust verwandeln und auf einer guten Datenbasis neue, umsatzstarke digitale Geschäftsmodelle entwickeln kann. Das ist ein Wettbewerbsvorteil gegenüber allen noch konventionell agierenden Anbietern! Auf perfekter Fernüberwachung basierender After- Sales-Service wäre beispielsweise so ein Modell.
Dabei werden die zugehörigen Ersatzteile entweder aus der digitalen Stückliste oder einem 3D/2D-Katalog selbstständig ausgewählt und auf Basis der angereicherten Maschinendaten und der Nutzungsdauer automatisch als Bestellvorschlag bedarfsgerecht bereitgestellt. Alles passiert online, nur der Lieferservice bleibt analog. Der Ersatzteilservice bleibt dort wo er hingehört. Beim Hersteller, mit der Expertise und dem langjährigem Spezialwissen über alle Maschinen und Anlagen im Feld. Den Kunden und den Herstellern erspart es vor allem Zeit und Rechercheaufwand. Denn die Informationen zur Anlage und den benötigten Ersatzteilen sind zentral an einer Stelle erfasst. Vor allem den Kunden dürfte es gefallen.
Auf die Schaltzentrale kommt es an
Wer Maschinen weltweit auf diese Weise betreuen will, braucht eine Schaltzentrale. Natürlich muss sie cloudbasiert sein, alles andere würde an der Datenmenge scheitern. Die EquipmentCloud® des Dresdner Software-Unternehmens Kontron AIS ist eine solche Schaltzentrale. Die IIoT-Plattform wurde zur umfassenden Dokumentation und Integration sämtlicher Maschinendaten für alle denkbaren Einsatzzwecke entwickelt.
Die EquipmentCloud® kommuniziert über den universellen Webstandard REST. Bedient werden können damit Maschinen und Anlagen aller Art, egal mit welchem Maschinenprotokoll sie arbeiten, vorausgesetzt sie kommunizieren mit der richtigen Schnittstelle. IoT-Geräte mit flow-basierter Programmieroberfläche ermöglichen eine einfache und flexible Datenübertragung der Maschinendaten – egal ob die Maschinen mit dem Webstandard REST ausgestattet sind oder ohne nicht. Auch wie viele Maschinen, welcher Art dabei integriert werden und an welcher Stelle in der Welt sie arbeiten, ist unerheblich. Singapur, Chicago, Köln oder Toulouse – die Bündelung in der EquipmentCloud® ermöglicht das Management global verteilter Maschinen und Anlagen. Es handelt sich dabei um eine abgesicherte Public-Cloud-Lösung nach dem Multi-Tenant-Prinzip. Niemand außer dem Maschinenbauer und dessen Endkunden (Betreiber) haben Zugriff auf die Daten.
Der Software-as-a-Service Anbieter Kontron AIS und auch der Plattform Betreiber Oracle haben keinen Zugriff auf den Kundencontainer samt verschlüsselter Daten. Für zusätzliche Absicherung sorgt ein ausgeklügeltes Nutzer- und Rollenkonzept auf Basis individueller Zugriffsrechte, Sichtbarkeitslevel und Applikationsrechte. Außerdem stehen die Server in Frankfurt am Main. Die Datenverwaltung unterliegt also dem EU-Recht und lässt sich individuell vom Maschinen- und Anlagenbauer, bzw. dessen Endkunden ausgestalten.
Alltagstaugliche Nutzung – ab sofort
Der Zugriff auf die Maschinendaten erfolgt mittels Webbrowser, Tablet oder Smartphone. An der Peripherie der EquipmentCloud® befinden sich ein Dutzend interaktiver Apps. Sie greifen unter den oben genannten Nutzungsszenarien auf die Daten zu. Die App RemoteAssistance ist eine von ihnen. Womit wir wieder beim Ausgangsthema wären – ohne jedoch das ganz große Thema zu verlassen. Denn eine Lizenz für die EquipmentCloud® erwerben und die Grundfunktion von RemoteAssistance nutzen, das geht auch aus dem Homeoffice heraus. Damit wäre der Grundstock gelegt – und die Qualität der Fernüberwachung ist schon in dieser ersten Ausbaustufe besser als die der meisten anderen Angebote. Möglich werden damit „Service Calls“ zwischen dem Servicetechniker des Betreibers und dem des Maschinenbauers.
Es handelt sich um Hilfe zur Selbsthilfe per Videotelefonie – mit sicherer Übermittlung von Dokumenten, Bildern und Chats. Ein zusätzlicher Videoassistent erlaubt per Datenbrille den Blick in die Maschine. Auch Schnappschüsse mit Whiteboard-Funktion sind möglich. Das Telefonat wird aus der Cloud heraus vom Instandhalter an der Anlage ausgelöst; der Servicetechniker des Herstellers erhält eine Benachrichtigung über den eingehenden Serviceanruf und kann sich unmittelbar auf die Maschine verbinden sowie direkt live Unterstützung leisten und kann dabei ganz ohne Dienstreise den Kunden bei der Problemlösung unterstützen.
Die verknüpften Apps dienen dabei als Backend, Informationsquelle oder Referenz. Am Ende werden alle ausgetauschten Daten in der App gespeichert. Die Ergebnisse aus der Lösungs-Session zwischen Kunde und Hersteller können direkt dokumentiert abgelegt werden und befüttern damit eine Datenbank, zum abteilungsübergreifenden Wissensaustausch über die Anlagen im Feld.
Hilfe zur Selbsthilfe – diese mit Wissen gefüllte Datenquelle gibt dem Kunden bei erneut auftretender Problemstellung die Möglichkeit sich selbst zu helfen und ermöglicht dies auch weiteren Anlagenbedienern.
Die zweite Ausbaustufe
Mit der High-End-Lösung RemoteSupport langfristig für erweitertes Servicepotential nach der Krise sorgen: Sie erfordert entweder die Einrichtung eines hardwarebasierten VPN-Clients (z.B. PCI-Karte, Router, etc.) in jeder Maschine und eines lokalen IoT-Gateways (verschlüsselter Internet Protocol Security (IPsec) VPN-Tunnel) beim Maschinenbauer oder als reine Softwarevariante die Installation eines VPN-Server in einer cloud-basierten VM sowie eines softwarebasierten VPN-Clients auf der Maschine oder dem angebunden IoT-Gerät. Darüber hinaus sind für beide Varianten das Aufspielen entsprechender VPN-Clients auf dem Desktopgerät oder mobilen Endgerät des Servicetechnikers notwendig.
Damit stellt die EquipmentCloud® eine direkte Verbindung („Tunnel“) zwischen den Netzen des Anwenders und des Maschinenbauers her. Die Auswahl der Endgeräte ist dieselbe: Tablet, Smartphone oder Desktopgerät, aber nun ist ein temporärer Direktzugriff auf die Maschine möglich. Damit sind Parametrierung, Konfigurationen an der Maschinensteuerung, umfassende Fernwartungen, Live-Tests oder Firmware- und Software-Installationen durch den Maschinenbauer möglich, wobei der Endkunde die Datenhoheit über seine Maschinendaten hat und im Einzelfall dem Maschinenbauer einen individuellen Zugriff auf die zu wartenden Anlagen geben kann.
Über die passende Remote Desktop Applikation müssen sich die Nutzer dabei keine Gedanken machen, da diese in einem initialen Setup für das System bereitgestellt und im Servicefall dynamisch zugeordnet werden. Nur die applikationsrelevanten Ports werden für die Wartung freigeschalten. Die Verbindungen werden dabei mitgeloggt. Dies ist besonders für den Maschinenbauer eine gute Nachricht, kann er doch so serielle Serviceanfragen und akute Kundenprobleme weltweit effizient abarbeiten, auswerten und abrechnen.
Übrigens, abgesehen von der aktuellen, aus der Not erwachsenden Begründung für die Fernüberwachung gilt auch die klassische von vor der Krise weiterhin: Remote Service spart Reisekosten, hilft Personalengpässe vermeiden und ist auch noch klimafreundlich. Eine Krise hilft manchmal auch neue Wege zu gehen.
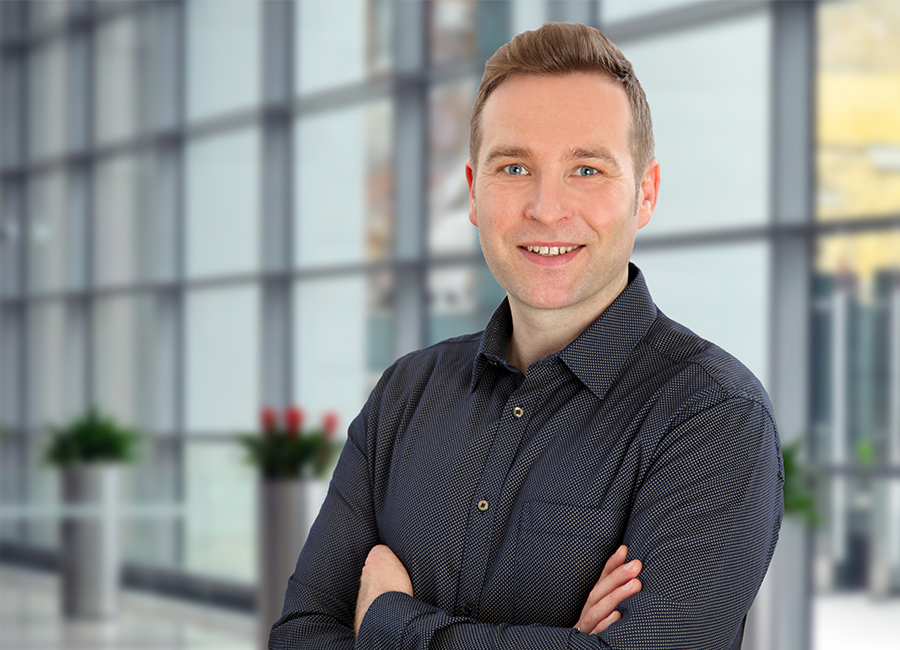